摘要:以一臺進口大型注塑機為對象,綜合運用機械學、液壓傳動以及控制理論,對注塑機的運動控制、動力傳遞控制、溫度控制以及控制系統構建進行深入研究,并利用可編程計算機控制器( PCC) 作為硬件設計一個全新的高性能控制系統,提高設備的綜合性能和自動化程度。
關鍵詞: 注塑機 可編程計算機控制器 控制系統 設計
早期注塑機控制系統普遍存在元件老化、故障率高和性能落后的缺點,利用現代控制技術開發精確、高效、節能型控制系統,延長設備壽命,解決這些設備在使用中的實際問題,是我國廣大注塑機用戶急需解決的問題。以一臺20世紀70 年代進口的大型注塑機為對象, 探討新型的注塑機控制系統的設計問題。
1 注塑機控制的方法和原理
注塑機的控制要解決的主要問題包括:機械運動控制、動力控制、溫度控制等。
1. 1 機械運動控制
機械液壓式注塑機是目前塑料行業廣泛使用的注塑機,它的機械運動控制的重點是開合模運動控制。雙肘式開合模機構運動原理如圖1所示。
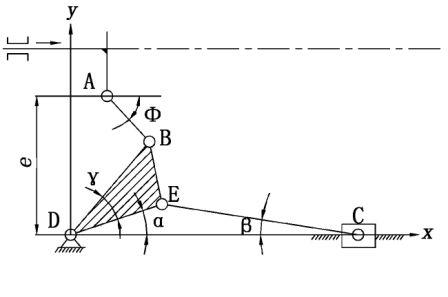
圖1 雙曲肘合模機構運動原理圖
開合模運動控制的對象是動模板C ,而動模板是由油缸通過雙曲肘機構驅動的,因此,需要建立油缸活塞位置與動模板位置的相互關系,以及油缸活塞在某一位置時活塞運動速度(由液壓系統開合模油缸流量決定) 與動模板運動速度的相互關系,即進行合模機構的線性化工作。
根據圖1 所示的運動原理,可以確立開合模油缸活塞與動模板的位置和速度的關系。控制系統軟件中,以一個通用線性化子程序實現這部分的運算,以便進行準確控制。
為減少CPU 的運算負荷,提高控制系統實時性,比較好的做法是以上述關系為基礎,編制計算機軟件,計算出活塞與動模板運動的一一對應關系,形成數據模塊,開合模運動控制時從數據模塊中直接讀取活塞和動模板的關系。
1. 2 動力控制
注塑機的動力傳遞以液壓傳動為主,注塑機的動力控制,要解決好兩方面的問題:一是壓力和流量的控制,它是決定設備精度的主要因素;二是設計合理的工藝動作流程和液壓動作時序圖。
1.2.1 壓力流量控制
與現代注塑機采用比例閥進行壓力流量連續控制不同,早期注塑機液壓系統大多采用壓力流量組合式離散控制。大型注塑機的多級壓力控制閥,是由6 個控制電磁閥組合動作,線性疊加進行壓力控制,因此,首先需要測定控制電磁閥對控制壓力的貢獻(壓力權) 。
通過實驗測定,6 個電磁閥的壓力權分別為: P1 = 0.218 75 MPa ; P2 = 0.437 5 MPa ;
P3 = 0.875 MPa ; P4 = 1.75 MPa ; P5 = 3. 5 MPa ; P6 = 7. 0 MPa 。
多級壓力控制閥的控制工作壓力P 可以用以下式表示:
P = K1 P1 + K2 P2 + K3 P3 + K4 P4 + K5 P5 + K6 P6 (1)
K1 ~ K6分別表示6 個多級壓力控制電磁閥的開啟系數, 取值0(不通電動作) 、1(通電動
作) 。
根據式(1) ,使用循環判斷的算法很容易實現根據設定壓力自動確定多級壓力控制閥電磁閥的動作組合。
流量的控制與壓力相類似。
1.2.2 工藝動作控制
對設備的工藝動作設計如圖2 所示。
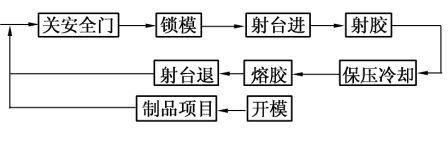
圖2 注塑機的工藝動作流程
設計液壓系統動作時序圖,就是要確定工藝動作對應的閥門動作邏輯順序。不同系統不盡相同。
1. 3 溫度控制
注塑機的溫度控制,主要是指料筒溫度控制。參數自整定PID 控制是現代注塑機使用較多的控制方式。系統設計分為如下步驟:
(1) 溫控系統硬件的設計。把料筒分為7個控制溫區,各溫區使用溫度傳感器( K 型熱電偶) 探測溫度,信號經放大、A/ D 轉換(由B&R PCC 2003 家族的模擬量輸入模塊A T 664 實現) 后輸入到PCC ,PCC 進行運算及處理后控制7 組控制器件(接觸器或無觸點過零型固態繼電器SSR) ,從而控制電阻加熱器對料筒加熱。
(2) 料筒溫控模型識別。研究結果顯示,料筒溫控數學模型可表示為一階慣性加純滯后環節,如式(2) 所示。
(2)
式中, t 為溫度,u 為功率,τ為系統時滯,Kt 為系統時間常數,K 為系統常數,s 為拉氏變換因子。
數學模型各參數可采用階躍響應法測得,見表1 。
表1 料筒各加熱段數學模型參數
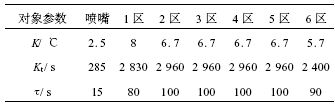
(3) 算法設計。確定參數自整定方式和PID 算法,采用參數繼電自整定和增量式PID控制算法, 這方面的理論不少資料有詳細的介紹。
2 注塑機控制系統的設計
下面以前面對注塑機控制的分析為基礎,采用B&R 公司出品的可編程控制器為主體,構建注塑機控制系統。
2. 1 硬件系統
控制系統硬件配置方式采用現代高檔設備通用的上下位機結構。上位機為操作監控制部
分, 采用帶486DX2CPU 的IPC2001 , 安裝了B&R Automation Runtime V2.60 操作系統,TFT 真彩屏,面板附帶注塑機專用30 鍵小鍵盤。下位機包括PCC 控制器及擴展模塊,其配置主要考慮滿足控制系統的現有功能需求,同時,適當預留功能擴展的需要。
由上、下位機構成的大型注塑機控制系統硬件組成及相互關系如圖3 所示。
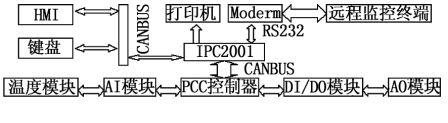
圖3 系統硬件組成
2. 2 軟件系統
2.2.1 任務設置
控制系統軟件主要由上位機和下位機軟件構成。上位機控制系統軟件需要實現顯示、通訊、數據存儲、配方的讀取和設置等功能,包括4大部分:程序模塊、系統模塊、數據模塊及面板程序模塊。下位機軟件系統是整個注塑機軟件系統的主要部分,它是按注塑工藝流程編寫的應用程序。B&R PC 操作系統Automation Studio(AS) 是一個分時多任務操作系統,采用分時多任務機制構筑其應用軟件的運行平臺。它可以把任務分成數個具有不同優先權的等級,其中優先權高的任務等級有著較短的循環掃描時間,而且每個任務等級可包括多個具體任務,在這些任務中間可再細分其優先權的高低。在AS 操作系統管理下,優先權高的任務總是先被執行,剩余的時間再執行優先權較低的任務。因此,在軟件設計中可以按應用程序的重要程度進行任務設置,從而使控制系統得到優化,具有較好的實時性。主要功能任務設置如表2 所示。
表2 主要任務級別設置
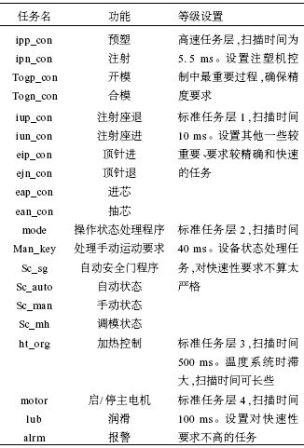
2.2.2 軟件組織結構
軟件系統用C 語言編寫,采用結構化設計,組織結構采用金字塔形由上至下4 個層次的層
級結構(如圖4) 。
第1 層為組織層(主程序mode) ,進行注塑機動作狀態的判斷和處理;第2 層為注塑機各個
狀態(全自動、半自動、手動、設置、調模狀態) 的運動組織和安全判斷的互鎖操作(動態互鎖和靜態互鎖);第3 層為各個動作或功能,它由第2 層進行組合調用;第4 層是指系統的壓力流量控制任務。
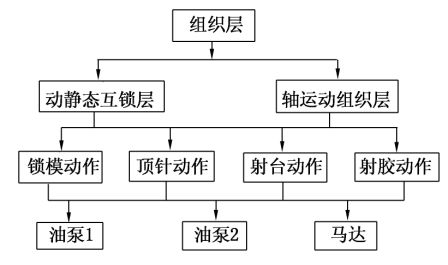
圖4 主程序功能框圖(部分)
3 運行結果
新設計的大型注塑機控制系統在投入生產后,在各方面顯示出比原控制系統更加優越的特
性,包括以下幾個方面。
(1) 分時多任務可編程計算機控制器(PCC) 的應用,解決了傳統PLC 控制系統掃描速度受制于程序大小的缺點,保證了注塑機控制的實時性和精確性。
(2) 基于各個任務的重要性不同與特殊要求,進行任務級別的科學分配,在保證了注塑機功能全面實現的同時,確保了關鍵過程控制的快速性與準確性。
(3) 高級語言(標準C) 結構化的程序設計,使系統具有更好的維護性與可擴展性。
(4) 功能較齊全,滿足注射成型的的各種工藝需要。比較科學的控制算法,使壓力、流量控制精度較原系統高;完善的軸互鎖功能,使設備具有較高的安全性和可靠性。
(5) 整機自動化程度較高,溫度控制系統參數自整定,動態和靜態性能比常規PID 控制更優越。
本系統的開發,解決了舊注塑機在使用中存在的問題,對提高設備功能、延長設備的使用壽命具有重要作用。
參考文獻
1 徐寶林. 注塑機機電特性研究及控制系統設計: [ 碩士學位論文] . 北京:清華大學精密儀器及機械學系,2004
2 北京化工學院及華南工學院合編. 塑料機械設計. 北京:輕工業出版社,1986.165~220
3 齊蓉. 可編程計算機控制器原理及應用. 西安:西北工業大學出版社,2002. 43~54
作者:徐寶林(金羚電器有限公司,江門, 529040)