摘要:可編程計算機控制器(PCC) 是一種專為工業環境下應用而設計的工業計算機, 文章對這項技術及其特點進行分析, 并以某熱電廠機組設備系統改造為例, 介紹了PCC這項技術在發電廠實現智能分布式數據采集和監控改造運用情況和效果。
關鍵詞: PCC;監控; 系統; 應用
0. 引言
隨著國民經濟的發展, 電網容量和用電負荷的日益增長, 電力系統對自動化和可靠性的要求越來越高。電力系統自動化對可靠性的需求, 使人們注意到"PLC" (可編程邏輯控制器) 這種高可靠性和強抗工業干擾的技術。90 年代以來, PLC 發展迅猛且應用的局域網技術日趨成熟, 產品不斷向系列化、標準化發展, 在自動化控制領域中, 新一代的PLC改名為PCC 已逐漸躍居主導地位, 成為實現自動化控制的關鍵技術, 在電力系統也不例外。
PCC( Programmable Computer Controller) 是一種可編程計算機控制器, 它是專為在工業環境下應用而設計的工業計算機, 采用"面向用戶的指令" , 因此編程方便;它直接應用于工業環境, 具有更強的抗干擾能力、更高的可靠性、廣泛的適應能力和應用范圍;大容量的存儲能力、標準通信接口, 基于過程總線的系統互聯、高級語言開發和運行環境,自診斷能力, 都使得PCC 在電力系統的應用具備了出色的友好"平臺"。
1. PCC 系統CPU的特點
繼承了PLC 與微機技術的PCC 技術形成第一代自動化軟硬件平臺結構, 采用32 位CISC 和
RISC 的CPU, 多處理器結構。圖1為本系統所用的CPU 模塊結構。圖中除了主CPU 外, I/ O - Processor 即I/ O 處理器主要負責獨立于CPU的數據傳輸工作。DPR - Controller 即雙向口控制器主要負責網絡及系統的管理。一個模塊上的3 個處理器,既相互獨立, 又相互關聯(通過DPR) , 從而使主CPU 的資源得到了合理使用, 同時又最大限度地提高了整個系統的速度。
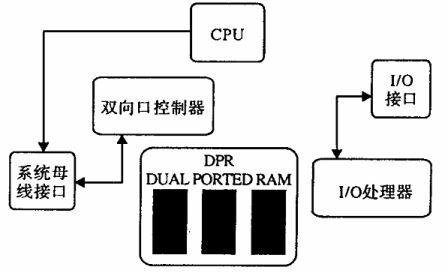
圖1 CPU模塊結構
2. PCC 在發電廠監控中的應用
以某熱電廠機組設備改造為例, 介紹應用PCC 實現的智能分布式數據采集與監控系統。該
熱電廠有大小機組7 臺, 裝機容量194 MW, 現準備對主要的4~5 號機及整個電氣系統進行監控系
統改造。
2.1 設計原則
系統按分布式結構設計, 采用開放系統、分層控制等先進的計算機設計思想, 將計算機技術、通信和網絡技術、數據庫技術、圖形和圖像技術、多媒體技術、數據采集和自動控制技術有機地結合在一起, 技術成熟, 運行經驗豐富, 能夠滿足近期的功能要求和遠期的發展需要。整個設計遵照國際90 年代IEC1000 系列標準, 滿足ISO9001 國際標準。
(1) 整個系統分為5 個采集控制站, 計有4 號機組監控、5 號機組監控、35 kV 出線監控、同期控制、01/ 1~3 號機/ 6 kV 監控。兩個操作員工作站。
(2) 通過計算機對勵磁調節器( KFD) 、發電機有功進行遙調。在4、5 號機控制屏上設有手操有功調節和KFD 無功調節及與汽機聯系指揮信號。
(3) 不含同期點的出線, 原控制回路取消, 采用計算機控制。含有同期點的出線, 應用成熟的計算機同期裝置, 采用計算機控制。
(4) 事故音響, 預告信號原回路取消, 功能由計算機系統實現。
(5) 廠用電BZT功能由計算機實現, 對4、5號機強行勵磁及主變風扇啟動控制均由計算機來進行判別控制。
2.2 系統結構
系統的網絡結構系統配置如圖2 所示。
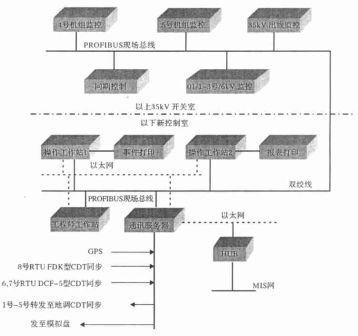
圖2 系統配置框圖
2.3 系統管理層
操作員工作站、工程師工作站和通訊服務器組成智能分布式系統結構的管理層。
管理層通過PROFIBUS 網絡與5 個PCC 采集控制單元相連, 各工作站和服務器分別相當于
PROFIBUS 網上的一個獨立的結點。
管理層采用多機及雙網絡方式運行, 各工作站及通訊服務器之間還組成一個小的局域以太網,實現數據的傳輸與共享, 互為備用, 提高了系統的可靠性; 軟件平臺采用32 位多任務、多進程設
計, 可支持Windows95/ 98/ NT操作系統軟件, 配有多種應用軟件接口, 并支持OEM開發, 為用戶提
供了二次開發平臺; 硬件平臺可采用小型機、微型機或工作站等設備。
通訊服務器完成與地調、模擬盤、GPS 天文時鐘接收裝置以及電廠已有的幾臺RTU 設備的通
信;還通過HUB 與該廠的MIS 網相連, 實時監控系統與管理信息系統結合在一起, 實現了實時信息的管理。
若用戶具備與Internet 連接的條件, 管理層還可以提供PVI 瀏覽器方案, 實現遠方讀取數據。
2.4 系統控制層
PROFIBUS 網上的各采集控制單元組成智能分布式系統結構的控制層。控制層按照機組或線路等監控對象的不同分別組屏, 可以使各單元組合置于過程對象附近, 減少電纜投資。各監控單元分別完成相應監控對象的模擬量、數字量采集以及數字量的輸出控制。模擬量采集采用交流采樣。
系統具有可擴充的模塊化結構, 電源、CPU、網絡板、I/ O 板、模擬量輸入板、通訊板等都是獨立的模板以總線方式連接在底板上, 它取代了標準的框架裝配的局限性, 可在標準的DIN 軌道上任意拆裝、組合。
每個單元都有一電源模塊。系統電源是系統可靠性與完整性的第一保證, PCC 的輸入電壓有
AC、DC兩種, 可實現交/ 直流切換。
系統配有當地調試通信口, 便于對不同的數據采集與控制設備進行跟蹤與調試, 方便了參數設置及運行監視的維護。帶電插拔采集板件使得現場維護變得簡單方便。
在軟件支撐環境方面, PCC 采用高級語言編程, 為用戶提供透明的服務接口, 同時, 也支持直流采樣, 使得功能實現、系統增容都十分方便靈活。
操作系統為實時多任務系統, 在操作系統中一個任務的循環周期可根據任務的優先級確定。操作系統主要分三層:
(1) 操作系統核。
(2) PCC 軟件包。包括: 系統管理、系統任務、功能庫、一般任務、高速任務級、通訊軟件。
(3) 應用程序。包括: 循環任務、非循環任務。操作系統為保證系統的高可靠性提供了監視和安全的功能, 包括: 模塊檢測、系統結構檢測、棧溢出檢測、I/ O 數據傳輸檢測、循環周期檢測、硬件看門狗等。
由于PCC 的CPU 采用68000 + RISC 的32 位微處理器, 具有極強的運算處理能力, 可使大量運算、控制功能、保護功能分散在各智能單元, 大大提高了站內通信網的利用率, 使整個系統效率達到最高。另外, 系統軟硬件方面良好的自診斷功能,可把故障范圍減至最小。
2.5 現場層
智能分布式系統結構的外圍層為現場層, 包括采集層使用的傳感器、二次控制回路等。
現場層根據現場總線網絡傳輸速率快( ≥500kbps) , 軟硬件實現簡單的特點, 可以用CANBUS
(或RS485) 來連接廠內的其他自動化裝置如保護單元、故障錄波、無功補償設備等的主干網, 并通過現場總線網絡連接到采集層, 與上一層進行必要的數據通訊。
2.6 網絡通信
采用的PROFIBUS( Process Field Bus) 網絡是一種高速數據鏈路, 是具有標準通訊能力的開放式現場總線, 用于PCC 與PCC 之間, 或與其它接到本網絡上的智能設備(如顯示單元、上位機等) 間傳送數據和系統狀態。PROFIBUS 網絡作為傳輸速度最快的現場工業總線(500 kbit/ s~10 Mbit/ s) , 物理連接方式簡單, 既可以用雙芯屏蔽通訊電纜, 也可以用光纖等;多主多從的"Peer To Peer"方式, 采用Token Ring 結構, 網上最多可連入多達128 個結點, 最大傳輸距離達4800 m; 與第三方系統通訊方便, 兼容性能;可任意的增加和刪除網絡結點,而對其他結點和整個網絡沒有影響, 可靠性高。PROFIBUS 網絡協議符合德國國家標準DIN19245。
系統的CPU 模塊、專用的網絡模塊和通訊模塊( 本系統未使用) 提供了多種標準通信接口
( TTY, RS422 , RS232 , RS485 等) , 使得CPU 的局部I/ O 總線擴展、遠程擴展I/ O(通過RS485 電纜)以及CPU 間的現場總線組網非常靈活, 從而方便地實現系統縱向或橫向集成。
3. 系統改造后效果
應用PCC 實現的電廠機組設備改造, 充分發揮了可編程編輯控制器( PLC) 的標準控制功能和工業計算機的分時多任務操作系統的集成優勢, 不僅方便地實現了各機組、廠變、出線及同期控制單元的開關量和模擬量的采集, 而且其雙網絡結構的管理層、具有大型機分析運算能力的PCC 模塊組成的控制層均為實現發電機有功調節、同期控制、強行勵磁、備自投等回路的自動控制提供了可靠的保證, 從而使該電廠的自動化管理水平登上一個新的臺階, 為建立全廠信息監控和管理系統打下良好的基礎, 為電廠節能增效、提高供電質量開辟了更廣闊的空間。
4. 結束語
總之, 開放式系統平臺是當今電力系統自動化發展的方向。現代的PCC 與微機的發展相互滲
透, 它已是一種可提供諸多功能、成熟的用戶應用控制系統, 而不是一種簡單的邏輯控制器, 它已被開發出更多的接口與其它控制設備進行通信, 生成報告, 多任務調度, 可診斷自身故障及機器故障。基于現場總線的智能分布式的新型控制思想, 基于標準化的開放性和兼容性, 通用性和高度專業化的融合, 這些優勢使PCC 可以實現電廠的各種運行、分析與控制功能, 能夠滿足當今的電廠實現生產、管理自動化的需要, 而且具有很高的性能價格比。PCC 應用為電廠全面提高管理水平和經濟效益提供了廣闊的前景, 是一種值得推廣的可行性方案。
參考文獻:
[1] 曹虹. 面向未來的可編程技術[J]. 機電信息, 1998 , 1。
[2] 許繼剛.21世紀電廠監控和管理信息系統若干問題的研究[J].火電廠熱工自動化.1999 , 9。
作者: 廖為宏(1963 , 男, 江西南康人, 高級工程師,碩士, 從事電力系統自動化專業技術工作)浙江巨化集團公司熱電廠,浙江 衢洲 324004