汽車零件:從打標、包裝到運送都確保百分之百的質量跟蹤
作為全球最大的汽車零件生產商和供應商之一,Borg Warner公司不允許在生產過程中出現任何的差錯。公司最近推出了一款性能優異的全新產品,不僅需要確保其優秀的質量,而且要實現產品全程的質量跟蹤。
由于Borg Warner公司的許多流水線和機器已經安裝了康耐視的視覺系統,因此該公司決定繼續使用康耐視的相關產品。這一項目的具體實施由康耐視在法國西南部的系統集成合作伙伴-- Alema Automation公司負責。
挑戰:
每一件零件需要進行打標,并且要驗證打標的精確度和質量。每一件零件必須經過最終的驗證,在確保經過了相關的質量和安全控制之后,才能運送到客戶手中。
解決方案:
康耐視公司的In-Sight 5110和VisionPro,康耐視系統集成合作伙伴Esox公司的產品ESO’CR,以及康耐視的合作伙伴--泰尼福公司的微沖式打標機。
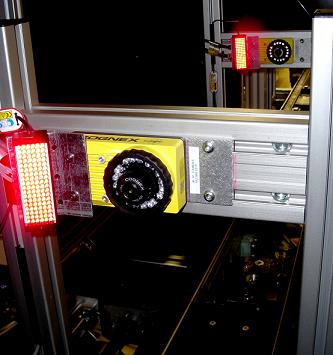
持久的打標效果
流水線生產的零件成品會進行微沖式打標,編碼由兩行的字母和數字符號組成,包含了產品碼、批量號、組識別碼(team identity)和生產日期。
經過打標工序之后,由8500采集卡和VisionPro(康耐視的視覺工具套件)組成的第一臺視覺檢測站,在ESO’CR軟件的協助下,讀取零件表面的編碼。此編碼信息被輸送到泰尼福公司的雕刻機,并被轉換成Datamatrix編碼,然后打標在零件的另一面。“ESO’CR軟件對汽車工業來說是一款行之有效的產品,因為它幫助我們有效的節省了時間和控制了預算。” Alema公司的項目領導Olivier Skalinski說到。
為了避免出現差錯和確保持久的打標效果,在微沖式打標機邊上同時安裝了In-Sight 5110,以此來驗證打標的精確度和質量。
如何確保每件零件都通過了檢測?
經過打標工序之后,零件會進入由8個檢測點組成的液壓測試環節。測試結束之后,零件被送入第二臺In-Sight 5110檢測站進行檢測,以此來確認每一件零件都成功通過了相關的測試。這一系列的過程是非常復雜的。
在各種環境下都能確保可靠的讀碼性能
進入第二臺檢測站的零件的表面可能是干燥清潔的,也可能帶有上一測試環節的油漬。盡管與第一臺檢測站的測試環境相比,零件表面編碼的照明和可讀性大不相同,但是In-Sight 5110系統無需額外的配置就能夠輕松的讀取零件表面的編碼。
Alema同時面臨了另一項挑戰:確保In-Sight系統能夠和儲存液壓測試結果的工廠數據庫進行通訊。因此公司開發了一款獨特的界面,使In-Sight對每一件零件做出適合/不適合運送的判定。
可修理的帶有瑕疵的零件被送回修理處,而成功通過驗證的零件則被直接送到包裝區。為了確保萬無一失,Alema在包裝區的入口安裝了第三臺In-Sight系統,對零件進行最終的驗證。
快速的部署時間
Alema以迅捷的速度開發和部署了該應用項目:公司用了兩天的時間確認該系統在模型零件上運行良好,然后用了一周的時間在工廠安裝系統,包括對員工進行系統的操作和維護方面的培訓。
強大的實力造就高性能的解決方案
由于In-Sight視覺系統功能強大,在零件的照明和位置不斷改變的情況下依然能夠保持優異的讀碼性能,因此該系統能夠勝任多種檢測任務,而且幫助Borg Warner公司顯著減少了庫存的備用零件數量。
該項目所體現的另一優勢是Alema Automation提供了全方位的解決方案,包括編碼讀取、打標和驗證,因此避免了不同供應商之間的利益沖突。
“得益于康耐視公司功能全面的產品和其廣泛的合作伙伴網絡,我們獲得了一項高性能、具有成本效益的解決方案。” Borg Warner公司的Stéphane Laval說到。
在此解決方案取得成功之后,Borg Warner公司將對其它流水線進行改造并部署相同的解決方案,從而在產品的生產過程中全面優化其質量跟蹤過程。