1 序言
真空均質乳化機(簡稱乳化機)主要應用于化工、醫藥、生物、食品等諸多領域中非均相液一固和液一液多相體分散體系的混合。目前該設備在國內主要是采用傳統的繼電器控制系統構成,操作人員需要根據經驗和儀表顯示輸入指令或數據進行手動操作,自動化程度不高,同時控制系統存在操作繁瑣、溫度控制超調量大、能耗高等缺點。
2 乳化機的工作過程
2.1 工作原理
乳化機由乳化鍋、水相鍋、油相鍋、真空裝置、溫度控制系統、電氣控制系統等組成。
生產工藝流程如圖1所示[1,2]。油溶性和水溶性原料分別在油相鍋和水相鍋內熔化或溶解,溫度一般保持在80℃左右,將用水蒸氣加熱的油相和水相原料通過過濾器加至乳化鍋內,以進行均質攪拌、乳化和真空脫氣。然后,向夾套通入冷水,冷卻到一定溫度后,添加香精,繼續冷卻至要求的溫度停止攪拌,待恢復常壓即可出料。
2.2 工作過程
(1)油相鍋、水相鍋進料后,啟動油相、水相攪拌電機,在線設定油相、水相電機的轉速;
(2)設定油相鍋、水相鍋控制溫度后,啟動油相鍋、水相鍋的溫度控制;
(3)當油相鍋、水相鍋內原料初處理完成后,啟動油相鍋、水相鍋出料泵,將初處理后的物料泵入乳化鍋內;
(4)當油相鍋、水相鍋內的物料完全泵入乳化鍋內后,出料泵停止運行。啟動液壓電機,垂直下降主攪拌器與均質攪拌器,當下降到位時,液壓電機停止工作,然后手動旋緊密封閥;
(5)當真空乳化鍋密封后,啟動主攪拌、均質攪拌電機。轉速將從零上升到用戶的設定值,并可根據不同的加工要求,在線改變主攪拌、均質攪拌電機的轉速;
(6)啟動真空泵電機,乳化鍋負壓力不斷變大,最終將達到用戶設定值;達到用戶設定值后真空泵電機自動停止;
(7)啟動乳化鍋溫度控制,自動對乳化鍋進行加熱控制,控制方法采用模糊PID恒溫控制,乳化鍋內原料將被加熱到用戶設定溫度;
(8)當乳化工作完成后,通過排氣口減小乳化鍋內負壓力,當乳化鍋壓力為零時,打開出料閥,排出乳化品。
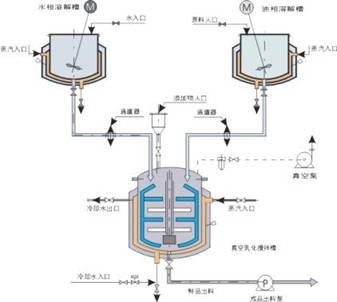
圖1 乳化生產工藝流程
3 控制系統的構成
3.1 控制系統的結構
根據系統設計要求,實現油相、水相、主攪拌、均質攪拌電機轉速控制,控制范圍依次是10rpm~1500rpm、10rpm~1500rpm、10rpm~80rpm、100rpm~4500rpm;實現油相鍋、水相鍋、乳化鍋溫度的智能控制,控制量范圍依次是:0~100℃、0~140℃、20~140℃;實現乳化壓力控制,控制范圍為-100Kpa~+100Kpa和液壓升降控制。
系統的結構如圖2所示。控制系統主要由上位機、下位機兩個部分組成,上位機采用臺達的HMI(DOP-B)[3];下位機采用臺達DVP48EH00R系列的PLC[4];電機的轉速控制,采用臺達VFD系列變頻器實現。
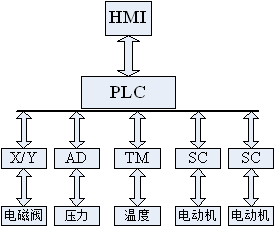
圖2 乳化機控制系統結構圖
3.2 控制系統的模塊劃分
系統的控制部分可以劃分為各種模塊,如圖3所示。
(1)壓力采集模塊
實現將壓力儀表的模擬電壓信號轉化為PLC可以識別的數字量信號,壓力表的信號通過PLC的AD(DVP-04AD-H)模擬量輸入模塊采樣到PLC中。
(2)溫度采集模塊
油相鍋、水相鍋和乳化鍋的使用鉑電極(Pt100)測量溫度,采用三線制接法。信號通過PLC的TM(DVP-04PT-H)PT100模塊采樣到PLC中。
(3)連鎖保護模塊
設置硬件和軟件雙重安全連鎖裝置,保證乳化鍋在抽真空的過程中不能打開鍋蓋,液壓站也不能啟動。
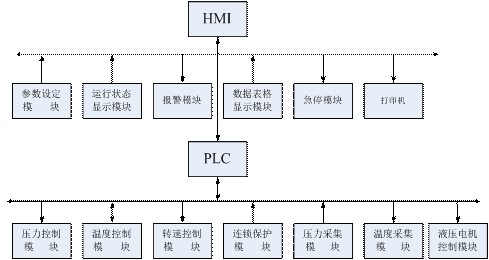
圖3 乳化機控制系統模塊圖
3.3 PLC容量選擇
乳化機控制系統的I/O點數分析見表1。
表1 I/O點數分析表
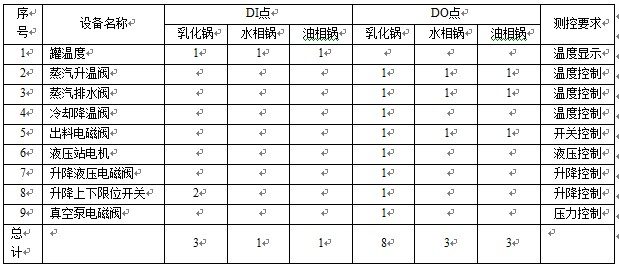
3.4 變頻器的選擇及通信
乳化機系統有主攪拌電機1個,均質電機1個,液壓站電機1個,真空泵1個,功率均為KW級,對于電能的消耗大,由于變頻器具有調速節能和軟啟動節能的作用,因此考慮選擇用變頻器。
本系統中選用臺達VFD-M和B系列的變頻器。根據人機界面上控制的轉速設定,輸出4~20mA的信號以調節電機的轉速,變頻器的運行需要和PLC進行MODBUS通信來確定是否啟動或停止。
4 控制系統的軟件設計
4.1 軟件設計的基本要求
操作功能主要是方便操作,需要人機對話界面。系統的規模越大,自動化程度越高,要求也越復雜,比如下拉式菜單設計、趨勢報警、I/O信息的顯示以及有關數據、表格的更新存儲和輸出等。圖4為設計的乳化鍋人機界面。
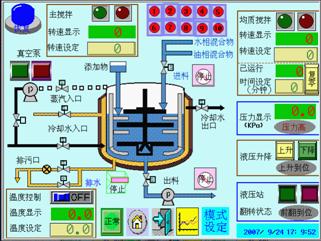
圖4 乳化鍋人機界面
4.2 I/O信號及數據結構分析
工業現場的檢測信號是多種多樣的,有模擬量也有開關量,PLC就以這些現場的數據作為對被控對象進行控制的源信息。通過對PLC的工作現場數據進行分析,確定了每一個I/O信號的地址。依據生產過程從前至后,I/O點數由小到大的原則把I/O信號集中編址。部分I/O信號的分配見表2。
表2 I/O信號的分配表
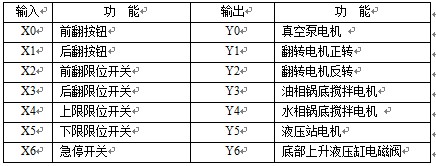
4.3 溫度控制
乳化機的溫度控制系統是以三個鍋的溫度為被控制參數,冷卻水流量為控制參數的回路控制。由于鍋溫系統是具有大滯后和時變性的系統,被調量不能及時反映系統受到的擾動,調節器的動作需經過一定的滯后時間才能影響被調量,經常會引起系統的響應超調過大或發生振蕩,導致系統過渡到其他操作狀態,用常規PID控制很難得到滿意的控制結果。
本控制系統采用臺達公司的DVP48EH00R系列的PLC為核心部件,實現恒溫控制,控制系統的原理框圖如圖5所示[5]。PLC根據采集的信號計算出偏差e(t)和偏差變化率ec(t),按照模糊PID的控制規則計算控制量u(t),并輸出控制量u(t)。經過PLC的D/A轉換,變成4~20mA的電流信號,送到調節閥來調節蒸汽或者冷卻水的流量,實現系統溫度的智能控制。

圖5 控制系統結構圖
5 總結
本文采用臺達PLC、HMI、變頻器設計了一套均質機自動控制系統,開發成本低、操作方便,能夠實現在線監視、控制和警報。目前控制系統運行良好,顯著提高了乳化控制系統的自動化程度,降低了控制系統的超調量,減少系統運行時間,有效降低乳化機能耗。