第1章 行業背景
石油企業是技術密集型、信息依賴型企業,石油行業的信息化一直伴隨著石油行業的發展,并發揮了巨大的作用。隨著“數字油田”、“數字石化”、“數字石油”等新的石油行業信息化理念被普遍接受,石油石化企業已經發展到了離開信息系統就無法生存的地步。
隨著近十年對現場自動化建設的加大,現場自動化的程度是越來越高,為數字化油田打下了良好的數據基礎。但數據僅僅停留在生產現場是遠遠不夠的,必須將分散在各地的油田數據匯集起來,提供給專家層、領導層,才能挖掘信息的潛在價值,將現場生產信息轉換為生產力。因此,建設一個經濟、高效、穩定、維護成本低的生產數據傳輸網絡就變得迫在眉睫,它是“數字化油田”的堅實基礎。
目前,數字化油田的發展面臨以下幾個方面的挑戰:
第一:設備標準復雜繁多。
標準是一個產業規模發展的前提,各個行業的標準復雜繁多。從通訊鏈路,涉及到RS-232/422/485、CAN、以太網、WIFI、Zigbee、GPRS/WCDMA/CDMA2000等;從工業設備協議來說,涉及到OPC、Modbus、IEC61850、IEC60870、DNP3、BACnet、PLC等。
第二:建設、維護成本太高。
數字化油田的目標就是為了解放人力,降低運行維護成本,而如果一個系統建設的成本高,實施周期長,維護成本高,那將是和數字化油田的初衷相背而馳的。然而現階段的工業生產監控類系統的建設卻是三高:設備數據的接入成本高,數據利用成本高,系統維護成本高。
第三:安全性差。
目前工業環境使用的傳輸協議多用在封閉,孤立的生產總線網絡環境下,為了通訊的高效便捷,多采用明碼傳輸,沒有任何的加密保護。容易受到來自網絡的各種攻擊。而數字化油田必然需要生產現場的設備數據通過Internet傳遞到遠端的另一個系統或環境中,因此,高效、安全的傳輸協議是實現數字化油田的一個必要條件。
第四:底層數據利用率低。
上層業務系統的數據要求導致底層數據傳輸系統的重復建設,致使數據利用率偏低。
因此建設可以智能組網、分布計算、路由優化、數據共享的工業數據傳輸系統將是推動工業智能的催化劑。同時也是數字化油田穩定可靠的保障。
第2章 目前普遍采用的解決方案
將自控系統接入到SCADA系統當中,屬于典型的兩化(信息化與自動化)融合項目。需要解決三個主要問題:
●自控系統的數據采集接口問題
由于自控系統相對比較封閉,接口方案各不相同。因此需要提供各系統的采集接口方案。
●自控系統安全問題
需要將控制系統與辦公管理網絡對接。由于管理網絡中可能存在影響控制網絡安全的因素,例如黑客或病毒等。這些不安全因素可能對控制系統帶來巨大的威脅,因此必須解決,確保控制系統100%的安全。
●遠程統一管理和維護的問題
由于項目現場涉及的控制系統具有數據多、類型雜、分布廣等特點,維護管理的難度非常大。需要考慮好建成后,管理和維護的問題。必須確保項目建成后,可以遠程實施統一管理和維護,以減少相關工作量,確保系統運行穩定,故障在第一時間可以遠程排查、直接解決。
目前的現場設備大多采用RS232/485等通訊接口,為了傳輸的方便,基本都采用了串口服務器(串口轉以太網)這類設備,這類設備直接將現場設備的通訊端口暴露到了網絡上,Modbus傳輸協議因為是為封閉的工業總線而設計,都是明碼傳輸,沒有任何的加密保護,容易受到來自網絡的攻擊。應用此種模式還會帶來以下幾點問題:
1) 串口服務器模式,串口服務器+臺式電腦+軟件。成本高,維護不便。SymLink工業物聯網智能網關集成了上述功能的嵌入式設備,成本低、部署靈活、維護方便。
2) 數據采集設備多采用標準PC計算機,體積大,不易上機架,占用機房空間大。并且PC計算機能耗高,穩定性較差,維護不便。
3) PC計算機大多采用Windows系統,容易受到操作系統漏洞,網絡病毒的攻擊,且對人為帶來的安全隱患難以防范,因此,總體安全性較差。
4) 如用于數據采集的PC計算機數量多,對這些計算機的集中維護管理,采集軟件的更新維護不便。缺乏一整套完善的中心管理方案。
5) 通過傳統的串口服務器,串口數據透明傳輸轉至以太網,數據都交給分行PC機計算,再由PC機軟件向總行傳輸數據,這樣每一級的相互依賴性過強。
第3章 采用SymLink構建的解決方案
工業現場的通信網絡依然由以太網交換機及路由器來搭建,以太網交換機及路由器只用于構建通訊的網絡,不關注現場設備業務數據的采集與傳遞;SymLink工業物聯網智能網關通過自身的各種通訊接口(RS232/RS485,CAN,以太網等)與各類現場設備直接連接,并通過現場設備的通訊協議采集需要的各類數據,同時將采集到各個設備的數據以標準工業協議(如OPC,IEC101/102/103/104,BACnet,DNP3,Modbus等)為上層應用系統提供,從生產現場到上層管理,為企業搭建了一套強壯、高速的業務數據傳輸網絡,幫助油田企業推進“數字化油田”的建設提供了堅實的基礎。
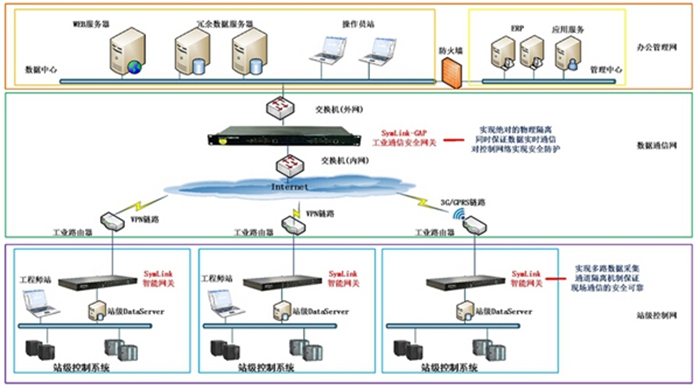
第4章 方案優勢
系統整體更加穩定可靠
分布式的數據采集計算方式,避免了集中式采集計算的單點故障,完全將集中式采集計算的系統負荷分化到各個采集節點。同時各個分布式的數據采集計算節點提供計算腳本,斷線緩存,報警服務等功能,即可為上層系統分擔計算負荷,又可最大限度的保證了業務數據的完整性和連續性。
標準化
對上層系統提供歸一化的標準協議,讓上層應用系統專注業務數據的分析應用,并提供各種實時/歷史數據庫及關系數據庫的無縫集成組件,一步到位。
兼容能力
廣泛的設備兼容能力,海量的通訊協議庫,提供工業現場各種主流設備的通訊協議驅動,如:OPC/Modbus/IEC61850/IEC60870/DNP3/BACnet/主流PLC/智能儀表等,并擁有一個10多人構成的通訊協議開發團隊,擁有多年的通訊協議驅動開發經驗,可以快速地開發出各類新推出的設備的通訊協議驅動。
安全性
站級控制網絡選用SymLink工業物聯網智能網關作為數據采集轉發設備,可實現多路數據采集轉發,并且采用白名單機制,可對通信協議進行過濾,使得符合用戶授權的控制系統實現安全的現場數據采集。
數據通信網絡層選用SymLink-GAP工業通信安全網關作為辦公網絡和控制網絡的隔離裝置,其2+1的產品架構可實現絕對的物理隔離,內網側采集控制網絡的數據,通過加密單向傳輸給外網側,進而將數據推送至辦公管理網絡。
無論是站級控制網絡還是在數據通信網絡,SymLink網關產品所具備的的通道隔離機制和物理隔離機制,均可為整套系統提供安全防護。
管理維護
深度挖掘用戶需求,集合多年的行業經驗,提供符合人性的圖形化的管理維護工具,企業IT工程師不需要參閱大量的文檔資料以及培訓,即可完全可視化的建立232/485/CAN總線設備的通訊以及以太網絡拓撲圖,輕松調用設備庫和模板庫即可完成工程應用。通過SymLink的網管系統(一套圖形化的設備集中管理維護平臺軟件),可將一個系統內的所有SymLink設備進行集中管理,配置,監視,維護。當系統中SymLink的數量越多、地域分布廣時,管理的設備越多,分攤給每個設備的管理維護成本更低。