柔性制造遇到的問題
我們觀察一個產品生產線就會發現,即使先進的集成產線,它也無法滿足個性化的生產需求。傳統的機械制造就是一個單元接著一個單元,輸送系統將被加工的對象送到加工單元進行加工,例如:沖壓、裁切、組裝、折疊、粘合、焊接等,在整個過程中輸送系統會將被加工產品由一個單元到另一個單元,那么這樣就會形成很多制約:
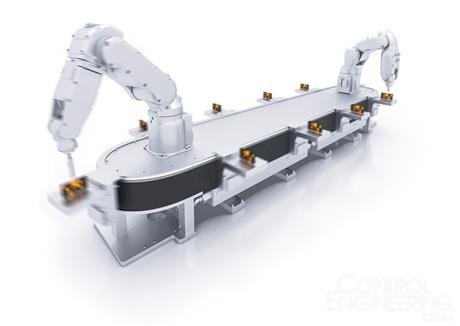
對于工廠而言,技術與概念并非他們關注的要點,End User通常只關心:
--如何讓產線獲得高的OEE
--少故障,穩定運行,即使出現故障,但易于維護;
但是,對于柔性制造而言,產品的個性化會帶來品質迭代的困難、換裝帶來交付能力的下降,過于頻繁的更換會在啟動/停機造成不良品,而對小批量生產會造成不良品率的上升。
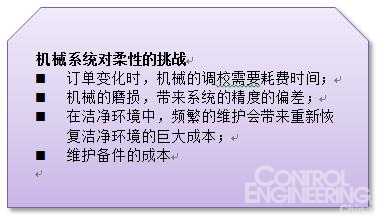
SuperTrak如何解決柔性問題?
其實,解決這個問題的辦法在于換個思路:傳統上加工工位是不變的,產品順著輸送系統傳送,這對于產品批量大、固定生產來說,無疑是正確的,但對于產品規格變化、生產工藝變化的個性化產品生產而言,則會遇到柔性問題,即機械如何不變來適應變化?
是的,讓被加工產品和工位都動起來,適應這種變化,SuperTrak即按照此思路來設計。
SuperTrak是基于長定子直線電機技術(LLM)所開發的柔性電驅輸送系統,它通過在定子上運行的變化的動子來改變被加工對象之間的尺寸,并與加工單元的設備如機器人激光切割頭、沖壓站進行同步,使得產品的尺寸規格、加工工藝變化時可以有更大的柔性來與加工設備進行配合,無需進行復雜的機械調校即可完成。
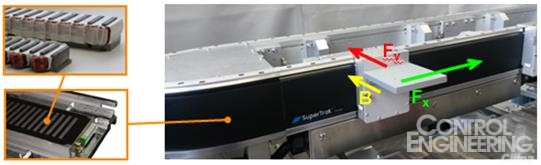
長定子直線電機 (LLM)
其目的在于:
(1)產品規格變化時,機械加工位置、間距的調校無需進行機械的調整,僅通過電氣參數的改變即可實現,尤其對于批量小而尺寸規格變化比較大的生產。
(2)整線速度可以具有較高的柔性,根據生產負荷的變化而變化。
(3)更高的集成度:產線的占地空間會變小,由于極高的電磁響應速度,使得無需為產品考慮堆積空間,而且加減速時間跟通過傳統變頻電機的方式而言響應速度非常高,因此,無需像傳統傳輸系統那樣必須設置較大的加減速空間。
(4)提升產線OEE。對于生產系統而言,OEE的下降包括了維護、訂單更換時的參數調校,傳統的輸送系統,尤其是電子半導體等領域的高精度產品制造,其工裝夾具精度較高,因此,調校會耗費時間、在調校過程中的產成品也會損失質量、機器的維護等都會影響整線OEE。
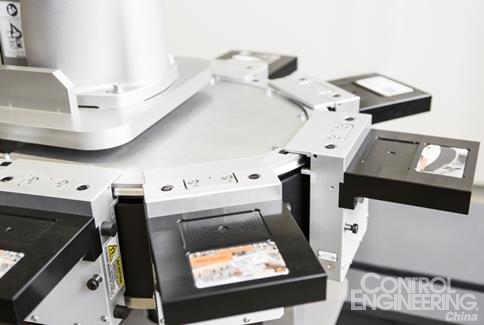
圖1-SuperTrak線性傳輸系統—如同F1的高速過彎
SuperTank可以實現達到10μm級的定位精度,并提供4m/S的生產線速度,而通過POWERLINK實時網絡可以提供高精度同步與定位控制。
顯著的優勢
由于采用的非接觸的方式,這給SuperTrak帶來非常大的優勢:
(1)高速響應:慣量極小的動子,實現快速的響應;
(2)無需減速機構:不存在傳統機械減速機構的背隙帶來的傳動精度問題;
(3)無需電纜拖鏈這些現場的部件;
(3)低磨損,易于維護—對于像食品制藥應用場景而言,這至關重要,因為每次進入潔凈區的維護作業都會讓恢復潔凈環境帶來新的成本。
仿真建模
數字化制造的核心是CPS-通過仿真對生產進行虛擬,包括控制工藝的參數優化、生產響應等,由于個性化生產必然沒有足夠的質量迭代時間和數量,因此,必須預先能夠對生產過程的參數進行優化,SuperTrak可以通過貝加萊的Automation Studio與MATLAB/Simulink、MapleSIM等軟件進行集成,仿真的結果可以直接運營于貝加萊的控制器。
SuperTrak的仿真建模可以將輸送系統、機器人、動子進行集成,對其生產過程的響應參數、調整、安全等進行完整的集成,包括抑制液體在運動中的波動。
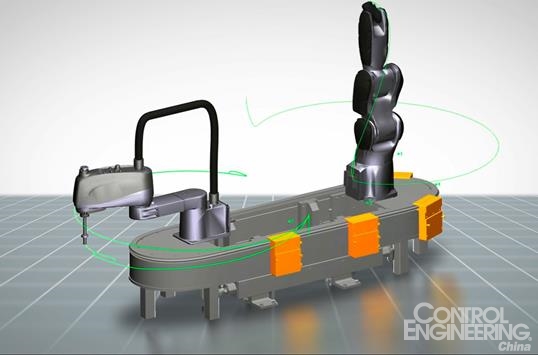
應用場景
SuperTrak適應于的應用場景包括:
(1)生產批量較小的產品,尺寸規模變化較大如疫苗生產、制藥與食品;
(2)需要潔凈環境,滿足制藥級潔凈要求的(采用不銹鋼制造);
(3)產線布局要求尺寸緊湊型的生產如電子、半導體生產。
目前SuperTrak支持10kg負載,達到50米長度的產線集成。